Gas Oxygen Technology (GOR) & other Science Research Technology
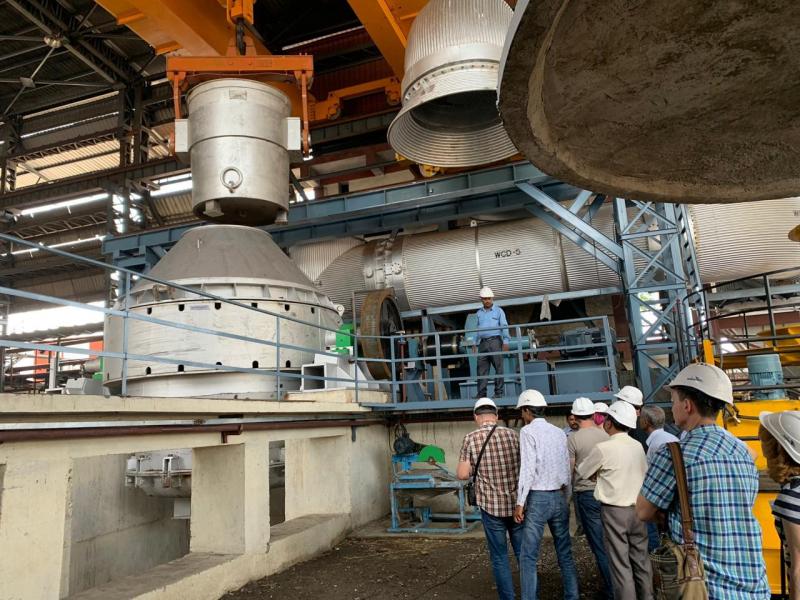
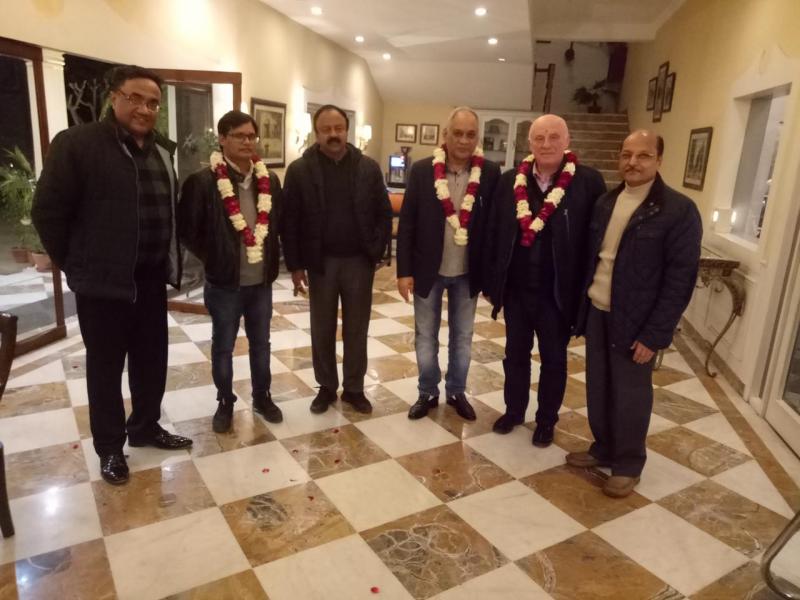
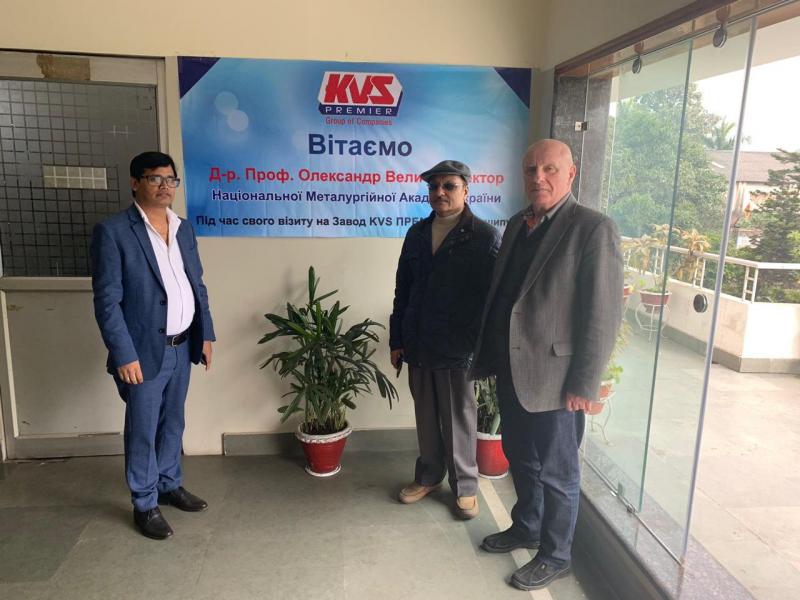
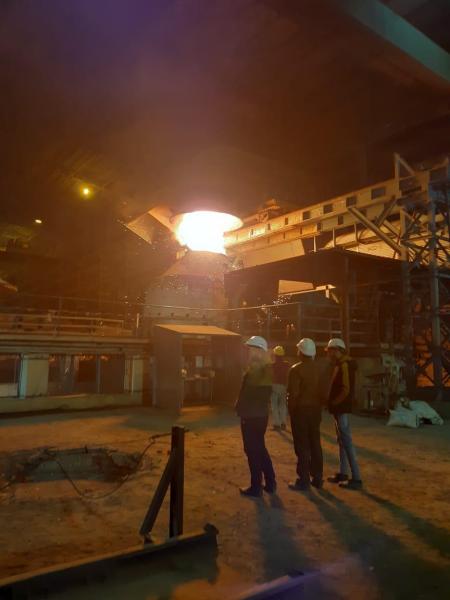
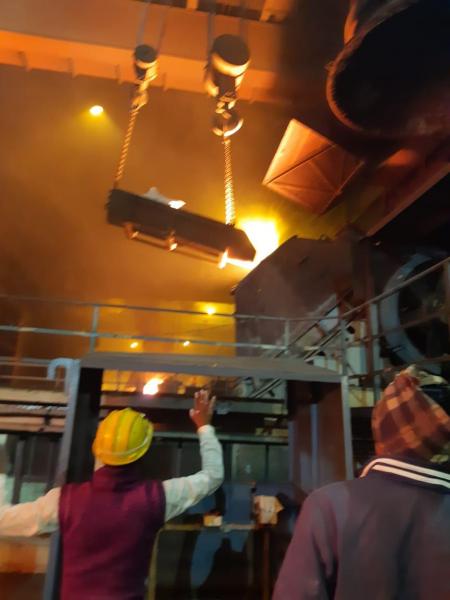
Prof. Alexander G. Velichko (Rector of NMetAU)
Dr. Mukesh Kumar - Director of Steel Research & Technology Mission of India "SRTMI"
Devendra Kumar Agrawal, Managing Director of KVS Premier Group
Alakh Singh - Assistant of the Rector of NMetAU (International Business)
Contacts: alakh@metal.nmetau.edu.ua | +38(093)709-66-82 (Whatsapp)
The patent rights for GOR technology and other technologies are with National Metallurgical Academy of Ukraine (NMetAU). It will design , develop software as well as sign the contract without any participation.
Innovative Resource-Saving Technologies in Steel Production & Gas Oxygen Technology (GOR)
- Extra-furnace treatment of iron-carbon melts for their refining and modification by electric arc depression.
- Production of corrosion-resistant steels by converter method (using gas oxygen refining process).
Representing technology: Corresponding Member of the National Academy of Sciences of Ukraine prof. Velichko O.G., Associate Professor Sadovnik Y.V., Assistant of the Rector of NMetAU (International Business & PhD running) Alakh Singh. - Converter bath blowing through double-layer tuyere.
- Super-low carbon steel melting and its extra-furnace treatment for producing high-plasticity steel.
- Deoxidation and extra-furnace treatment of steel for manufacturing high tensile strength wire rod in order to reduce breakage while drawing.
- The National Metallurgical Academy of Ukraine and the “Gas-Oxygen Refining Technologies” are the developers of gas-oxygen refining (GOR) technology, specialists conduct melting, write technology instructions, train factory personnel, possess “know-how”, have patents and own programs for melting for each steel grade (groups 200, 300, 400 – corrosion-resistant steels).
Gas-Oxygen Refiner (GOR) to make world-class stainless steel or grade of special steel
The scientists of the National Metallurgical Academy of Ukraine invented the Gas-Oxygen Refiner (GOR) technology in 1980's.
The GOR can be employed in the following metallurgical applications:
-
To make stainless steel in a duplex process involving induction furnace or EAF, using the scrap and ferroalloys
-
To remove sulphur & phosphorus and to refine the molten steel from the induction furnace / electric arc furnace
-
To produce ferroalloys (e.g. low phosphorus, low carbon ferromanganese)
-
To refine the rough, black & blister copper and also to refine the rough ferro nickel
-
To make mild steel, alloy steel or stainless steel directly from the molten iron produced in the blast furnace
Thanks to the converter nature of the GOR technology, minimum capital investments and minimum operational costs are required in the steelmaking stage of metal production.
The GOR can make various grades of alloy steels & stainless steels (301, 304, 304 L, 316, 316 L, 316 Ti, 321, etc.) as well as manganese group of stainless steel grades. The academy provides the design, engineering, automatic control system and both hardware & software technologies for the GOR, to make over 140 grades of steel.
The GOR method is universal. It can replace the traditional converter, ladle refining furnace and VD/AOD / VOD processes. In comparison with these technologies, the GOR has a higher efficiency, wider technological possibilities and generates the highest quality of final products at the level of the world's best standards.
When the capacity of the GOR is in excess of 15 tons, it can be combined with the continuous casting method. Smaller plants can employ ingot casting. GOR process time is 30-45 minutes, depending on the grade of steel. The total cycle time is 55-65 minutes.
An additional GOR feature is alloying the steel with nitrogen during the gaseous phase. After the melting process is completed in the electric arc furnace / induction furnace or blast furnace, the metal is transferred into this bottom- blowing converter, where 3 cleansing stages t ake place; decarbonization, recovery and desulphurization; and if necessary, metal alloying with nitrogen.
Corrosion-resistant steel produced by the GOR method, in comparison with the classic electro-metallurgical method, is much purer in its content & is virtually free from non-metallic particles & other residual impurities.
The GOR technology is also designed for the production of carbon steel, in case of a low demand for stainless steel.
The method of refining the steel in the GOR with a bottom or a combined blowing differs from other methods, by the high rates of all the refining processes. In comparison with the counterparts (AOD - argon-oxygen decarbonization and VOD - vacuum-oxygen decarbonization), the GOR method is characterized by high-performance; it increases the technological capabilities of the steel making process, and at the same time ensures the world-class quality of steel.
The GOR has low investment, low cost of production & high productivity to make high quality of special steels, thus creating good economic benefits to the customers.
The process uses a combined blowing technology to refine the steel.
The GOR main features include
-
High productivity - oxygen flow is used to refine the pre- steel with liquid carbon, which does not lead to the oxidation of chromium.
-
Lower Ar consumption - with the late blowing technology for argon, its consumption is reduced to 6-8 m3 per ton.
-
To save on the cost of the expensive low carbon ferrochrome, high carbon ferrochrome can be used.
-
Blowing time is short, i.e., only 30-45 minutes to make low carbon stainless steel.
-
High Cr yield - bottom blowing process improves the gas dynamics, resulting in Cr reduction of 97%.
-
Refining operations can be easily reproduced & controlled by the process control system. The GOR converter can quickly complete the tasks of decabonization, desulphurization, de-oxidation, degassing and alloying the steel. If necessary, it can also be used for dephosphorization.
Following are the advantages of the GOR, as against the AOD process to make stainless steel:
- The GOR can take high carbon ferrochrome (8% carbon) and has no limitations by initial carbon content. When high carbon ferrochrome is used in the GOR, 97-99% of the chrome is available in the stainless steel.
- The GOR needs less than 10 m3 of Ar (normally 6-8 m3) per ton of stainless steel, as against 20 m3 per ton in the AOD process. While making stainless steel in the GOR, Ar is blown in the end of the process for 5 min to reduce the loss of Fe and also to remove the hydrogen (residual hydrogen in the metal will be less than 2 ppm).
- The GOR can reach 0.01% carbon in the stainless steel, as against 0.02% in the AOD process. This is because oxygen is blown from the bottom of the GOR, as against from the top in other technologies.
- The Investment on the GOR is 2-3 times lower and includes the furnace, automation system (for 40 grades of steel) with Siemens hardware, ladles for metal & slag, feeding bins, gas cleaning system, supervision of erection & commissioning and plant training.
- While refining the metal from sulphur & phosphorus, the Fe lost in the slag is only 10-20%.
The GOR uses high MgO refractory. The refractory life is 150 - 200 melts. It takes 12 hours to re-build the refractory, after which the warm up takes another 30 hours. The design of the GOR enables its rotation by 360° to facilitate the pouring of metal & slag separately.
The GOR technology makes it possible to produce metal parts with set parameters of chemical composition and metallurgical properties.
The GOR advantages include
-
Capacity of the GOR can be as low as 3 tons or as high as 100 tons per charge
-
Possibility to realize both oxidizing and reducing conditions of refining during the steel melting
-
In the process of blowing the liquid metal by technical gas mixtures, the semi-steel product goes through the process of de-carbonization, which helps to achieve a higher degree of conversion of Cr (97%) & Mn (70%)
-
Possibility to make steel with specially low content of carbon (
-
Productivity increased by 1.5-2.0 times as compared to the AOD process, which allows reducing the investment costs for construction
-
Technological flexibility of the process allows the use of liquid half-products made of cheap scrap and high- carbon ferroalloys (without any limitation on the initial carbon content) or 100% stainless steel wastes
-
Compared to the AOD method, the GOR provides a significant (1.5-2.0 times) reduction in the consumption of expensive argon
-
The GOR method is universal, which not only allows melting the corrosion-resistant steels and alloys (including very low-carbon), but also practically all grades of high-quality steels including carbon, low-alloy and alloy steels
-
It is easily made possible to maintain the optimum temperatures & slag conditions of melting in the GOR, depending on the requirements of different grades of steel.
-
Slag and metal are tapped separately, which allows deep desulphurisation of steel and successful alloying with titanium and other readily oxidized elements these can be used for alloying or for modifying the finished steel
-
Possibility of alloying the corrosion-resistant steels with nitrogen in the gas phase up to the limit of its solubility. In steelmaking, when the nitrogen content is lower than its solubility limit, an accuracy of ± 0.01% of nitrogen mass fraction is achieved without the use of nitride ferroalloys
-
At the refining stage, non-ferrous impurities which have high vapor pressure compared to iron (such as lead, Pb, tin, Sn) are considerably removed, and deep degassing of the metal with minimum oxidation is achieved
-
Low consumption of refractories
-
Production of unlimited grades of steel, as per the market demand.
The above advantages of the GOR refining can be achieved by different capacities of the GOR converters and by different modes of blowing, depending on the steel grades produced and the technological stages of refining. The gas supply system of the GOR converter p rovides the supply and flow con trol over oxygen, natural gas, argon and nitrogen. The oxidation potential of the blowing can be modified in a range from 100% pure oxygen to pure inert gas.
Milestones of GOR installations
1987 - At the Electrometallurgical factory "Dniprospetsstal", the f irst industrial gas-oxygen refiner (GOR) with a capacity of 60 tons was implemented.
2002 - A 5 ton GOR unit was installed at Armaprom LLC (Mirgorod). Armaprom LLC specializes in the production of pipeline valves from corrosion-resistant steels.
2006 - The South-West Stainless Steel Company in Sichuan province, China, implemented the first GOR converter of 60 tons and produced corrosion-resistant Cr-Ni and Cr-Mn steels successfully. According to the post- launch da ta reported, the savings were roughly 200 USD per ton, in comparison with the smelts performed in the EAF.
2008 - At the Shangdong Taishan Steel Group factory, China, the workshop containing three 70 ton GOR converters was put into operation for the production of corrosion- resistant steels.
2009 - At the De Sheng factory, China, the workshop containing three 80 ton GOR converters was put into operation.
2012 - Started construction of a factory in Donggang, China, with three GOR converters of 10 tons each.
2013 - At the factory "Dnepropress", Ukraine, 3 and 15-tons GOR converters operate.
2018 - At the factory "Kashi Vishwanath Steels Pvt. Ltd. (KVS Premier Group), Kashipur, Uttarakhand,INDIA” 20-tons of GOR converter operate.
A summary of the GOR technology in the production of carbon “soft” steel using up to 50% of solid filling in the converter
1. Requirements for charge materials
The charge, alloying, slag-forming materials used in the GOR process are delivered in a container of the Customer’s plant and stored at the charge section of the gas-oxygen refining (GOR) department.
Loading of charge, alloying and slag-forming materials into the converter will be carried out with the help of a “scoop” with an electric bridge crane.
- Sponge iron*:
A typical composition of sponge iron is given in the table below.
Fe(M), % |
С, % |
S, % |
P, % |
SiO2, % |
81,5-83,5 |
0,09-0,18 |
0,029-0,04 |
0,055-0,075 |
4,5-5,2 |
* – according to the Indian side
- Carbon steel scrap*:
A typical composition of carbon steel scrap is given in the table below.
Fe, % |
С, % |
S, % |
P, % |
Si, % |
Mn, % |
97,4-99,6 |
0,036-0,22 |
0,003-0,01 |
0,014-0,033 |
0,02-0,59 |
0,167-1,03 |
* – according to the Indian side
- Carbon scrap (cast iron)*:
A typical composition of carbon scrap (cast iron) is given in the table below.
Fe, % |
С, % |
S, % |
Р, % |
Si, % |
Мn, % |
92,8-93,3 |
3,37-3,84 |
0,016-0,086 |
0,021-0,024 |
1,93-2,44 |
0,42-0,82 |
* – according to the Indian side
Storage of scrap should be organized strictly by types, depersonalization and mixing of various types of scrap is not allowed.
- Ferrosilicon.
On the converter redistribution it is recommended to use ferrosilicon with a silicon content of at least 65% with a particle size of 2 or 3. International Standard ISO 5445-80.
A typical composition of ferrosilicon is given below:
FeSi 65 |
FeSi 70 |
FeSi 75 |
|
Si |
63-67% |
68-74% |
75% min |
Сr |
0.02% max |
0.02% max |
0.02% max |
S |
0.05% max |
0.05% max |
0.03% max |
Р |
2.0% max |
2.0% max |
2.0% max |
Al |
0.2% max |
0.2% max |
0.2% max |
Mn |
0.4% max |
0.4% max |
0.4% max |
Сr |
0.4% max |
0.4% max |
0.4% max |
- Ferromanganese.
On the converter redistribution it is recommended to use ferromanganese of the following composition: Mn-78%, C-7%.
- Aluminum.
For this process aluminum ingots of AB97 and AB91 grades (GOST 295-98) should be used:
Mass fraction, %
Grade |
Sum of Al and Mg, not less |
Including Mg, not more |
Impurities, not more |
||||
Cu |
Zn |
Si |
Sn |
As |
|||
AB97 |
97,0 |
0,1 |
0,1 |
0,1 |
1,0 |
0,1 |
0,1 |
AB91 |
91,0 |
3,0 |
3,0 |
0,8 |
3,0 |
0,3 |
0,2 |
- Lime (freshly burned):
A typical composition of lime is given in the table below.
SiO2, % |
Al2O3, % |
CaO+MgO Ca total, % |
CaO+MgO Ca activ., % |
CO2, % |
MgO, % |
S, % |
Р, % |
3,1 |
0,85 |
92,4 |
88,3 |
1,2 |
0,28 |
not more 0,05 |
not more 0,05 |
- Dross*:
A typical composition of dross is given in the table below.
FeO, % |
Мn, % |
С, % |
S, % |
Р, % |
86,0-95,0 |
0,08-0,20 |
0,02-0,07 |
0,02-0,03 |
0,04-0,05 |
* – according to the Indian side
- Carbonaceous material (coal, coke, etc.).
It is recommended to use materials containing not less than 80% of carbon and not more than 0,5% of sulfur.
- Iron ore.
It is recommended to use ore containing at least 60% of Fe and not more than 0,04% of P.
2. Gas-oxygen refining
2.1. Charge materials for carbon (soft) steel in the GOR converter are liquid electric furnace intermediate product (from induction furnaces) and solid metal additives. Sponge iron, carbon steel scrap, cast iron, and ferroalloys are used as the latter.
2.2. The gas-oxygen refining process includes three main stages of melting.
2.2.1. At the first stage, a part of the solid filling, consisting partly of sponge iron and cast iron, is preheated and melted due to the burning of carbon in carbon-containing fuels (coal) and the oxidation of silicon in cast iron. Purging is carried out through bottom blowing devices with oxygen and protective (natural) gas. The intensity of the oxygen blowing is 1,5-2,0 m3/ton per min. The consumption of natural gas is approximately 8-10% (by volume) of oxygen consumption.
2.2.2. At the second stage, after melting of the solid part of the filling and pouring the liquid part (intermediate product from induction furnaces) of the melt, the metal is dephosphorized. Purging is carried out through bottom blowing devices with oxygen and protective (natural) gas. The intensity of oxygen blowing is 1,5-2,0 m3/ton per min. The consumption of natural gas is approximately 8-10% (by volume) of oxygen consumption.
At the final phase of the second stage, for intensive mixing of the bath, metal is purged with pure argon, which is supplied into both channels of the tuyeres with intensity 0,6-0,7 m3/ton per min.
During the purge, lime in the amount of 35-45 kg/ton is added to the converter bath.
If necessary, for acceleration of the processes of slag formation and improving the fluidity of slag, it is recommended to use fluorite concentrate (fluorspar, CaF2) in the amount of 10-15 kg/ton.
The temperature of the metal at the end of the stage is 1580-1620 °C.
2.2.3. If necessary, the phosphorus-free metal without slag that contains phosphorus (slag is removed from the converter to a slag pot, installed on a steel slag carriage) is additionally subjected to a desulfurization process. For these purposes, a new slag is induced. During this period, purging is conducted through bottom blowing devices with oxygen and protective (natural) gas. The intensity of the oxygen blowing is 1,5-2,0 m3/ton per min. The consumption of natural gas is approximately 8-10% (by volume) of oxygen consumption.
At the final phase of the third stage, for intensive mixing of the bath, metal is purged with pure argon, which is supplied into both channels of the tuyeres with intensity 0,6-0,7 m3/ton per min.
During the purge, lime in the amount of 30-40 kg/ton is added to the converter bath.
The temperature of the metal and at the end of the stage is 1680-1720 °C.
2.3. The addition of metal charge, lime, deoxidizing agents and other additives to the converter is carried out with a scoop.
Floor scales are used for weighing of solid additives.
2.4. Approximate duration of particular periods of gas-oxygen refining and supply of gases through the bottom blowing devices is following:
Name of operations |
Duration, min. |
Central nozzle |
Peripheral channels of tuyeres |
Filling of solid metal charge and slag-forming |
5 |
oxygen or nitrogen |
natural gas or nitrogen |
Stage 1 of purge |
25-35 |
oxygen |
natural gas |
Pouring liquid intermediate product |
5 |
oxygen |
natural gas |
Stage 2 of purge |
10-20 |
oxygen |
natural gas |
Stirring the bath with argon |
5 |
argon |
argon |
Phosphorous slag removal |
5 |
oxygen or nitrogen |
natural gas or nitrogen |
Stage 3 of purge |
15-25 |
oxygen |
natural gas |
Stirring the bath with argon |
5 |
argon |
argon |
Turn-down, temperature measurement, sample |
10 |
oxygen or nitrogen |
natural gas or nitrogen |
Production of finished steel |
3 |
argon |
argon |
Slag drain |
2 |
oxygen |
natural gas |
Total: |
90-120 min. |
3. Expenditure weights for the GOR process
Consumption |
Quantity, per ton of finished steel |
Oxygen (all technological operations) |
up to 40,0 m3/ton |
Protective natural gas |
up to 4,0 m3/ton |
Argon |
up to 5,0 m3/ton |
Nitrogen (used at turn-down of the converter) |
up to 10,0 m3/ton |
Lime |
up to 70 kg/ton |
Carbonaceous materials (coal, coke, etc.) |
up to 4 kg/ton |
Cast iron (С – 3,0...4,0%) or carbon-containing materials |
40-45 kg/ton or 2-3 kg/ton |
Aluminum ingots АВ97 and АВ91 grades (GOST 295-98) |
5-10 kg/ton |
Ferroalloys for deoxidation of steel: Ferromanganese (Mn-78%) Ferrosilicon (Si ≥ 65%) |
up to 6 kg/ton up to 15 kg/ton |
For heating of metal: Ferrosilicon (Si ≥ 65%) |
2,0-3,0 kg/ton |
For intensification of the dephosphorization process: Dross (or iron ore) |
20-25 kg/ton |
The yield – 85-90%
The degree of dephosphorization – 70-80%
The degree of desulfurization – 65-75%
The chemical composition of the finished steel, % wt:
С |
Mn |
Si |
S |
Р |
0,10-0,30 |
0,50-0,65 |
0,40-0,50 |
0,030 (max) |
0,040 (max) |
Nitrogen-alloying of structural and corrosion-resistant steels to increase their performance properties
The introduction of nitrogen into steel improves the quality of the metal and reduces the consumption of alloying materials such as tungsten, molybdenum, nickel, and others.
Two main tasks are solved during nitriding of steels:
- introduction of nitrogen into the melt and ensuring its concentration at the level of 150-250 ppm (0.015-0.025%) and higher.
- binding of nitrogen in steel into strong carbonitrides (nitrides).
The whole process is called carbonitride hardening, and the product – increased strength steels with carbonitride hardening.
The practice of nitrogen introducing into steel with an additive of nitrated ferrovanadium (FeV) in the steel-teeming ladle with steel production under the jet has become the most widespread.
Table 1a shows the composition of nitrated ferrovanadium.
Table 1a. The chemical composition of nitrated ferrovanadium.
Grade of alloy |
V |
N |
C |
Mn |
Si |
Al |
P |
Not more |
|||||||
ФВд45Н10Мнз |
40-45 |
9-11 |
0,75 |
3,0 |
2,0 |
1,0 |
0,1 |
ФВд40Н8Мн6 |
35-40 |
8-10 |
1,0 |
6,0 |
2,5 |
1,5 |
0,1 |
ФВд35Н6Мн6 |
32-35 |
6-8 |
1,0 |
6,0 |
3,0 |
3,0 |
0,1 |
The production of nitrated ferroalloys is quite complex and expensive with all the simplicity of the additive nitrated ferrovanadium and the recognition of the effective results of the carbonitride hardening of vanadium.
In this regard, researchers and practitioners are looking for an alternative to nitrogen introducing into steel with nitrated ferrovanadium and replacing the latter with more available ferroalloys that bind nitrogen to form nitrides.
1. Due to the capabilities of the GOR unit, it is proposed to saturate the metal with nitrogen by flushing with nitrogen through these forms, including:
- nitriding of carbon steels;
- nitriding of corrosion-resistant steels.
Binding of nitrogen into nitrides can be done with FeV (expensive production of nitrided ferrovanadium is excluded in the process chain).
2. The National Metallurgical Academy of Ukraine has developed a technology of additional micro-alloying of steel providing carbonitride hardening (increasing the strength of the billet in a hot-rolled state), making it possible to obtain a significant surplus value of a new grade end product (for example, reinforcing bar of B500C grade, high strength fasteners).
Table 2c shows the chemical composition of steel with carbonitride hardening by titanium and aluminum.
Table 2c. The chemical composition of steel Ст3сп with carbonitride hardening, % wt.
Alloy number |
С |
Mn |
Si |
S |
P |
Al |
Ti |
N |
166215 |
0,19 |
0,71 |
0,30 |
0,010 |
0,024 |
0,028 |
0,016 |
0,018 |
166908 |
0,19 |
0,63 |
0,28 |
0,014 |
0,015 |
0,029 |
0,003 |
0,020 |
After processing the wire rod into reinforcing bar according to the scheme in Fig. 1c. the mechanical properties of the reinforcing bar are presented in Table 3c.
Fig. 1c. The scheme of the technological line for processing the wire rod into reinforcing bar of B500C grade.
1 - unwinding device, 2 - descaler, 3 - roller cassette, 4 - drawing mill, 5 - winding device.
Table 3c. Mechanical properties of the billet (wire rod) and reinforcing bar.
Regulatory document |
Type of rolled steel |
Ϭт(0,2)9 N/mm2 |
Ϭв9 N/mm2 |
Ϭв/Ϭ0,2 |
Δ5 % |
Δр % |
Agt% |
Strength grade |
ГОСТ Р 52544 |
Armature rolling |
≥500 |
≥550 |
≥1,05 |
≥ 2,5 |
В500С |
||
Wire rod |
382 |
543 |
1,42 |
34,6 |
20,8 |
21,1 |
||
Armature rolling |
542 |
623 |
1,15 |
18,6 |
4,6 |
4,9 |
В500С |
The use of reinforcing bar in hanks with a yield strength of at least 500 N/mm2 in the building will ensure high efficiency of its use, reduce waste during processing, and also allow to organize industrial production of nets, frames and other reinforcement products for monolithic house building and industrial civil engineering. The result is a significant savings in electricity, labor and cost.
The mechanical properties of bolts made of steel with carbonitride hardening are given in the table 4с.
Table 4c. Mechanical properties of bolts.
Steel |
Condition |
Ϭ0,2 N/mm2 |
ϬВ9 N/mm2 |
Ϭ0,2/ ϬВ |
Δ5,% |
Strength class |
20кп |
No processing |
558 |
700 |
0,80 |
9,5 |
6,8 |
Ст3сп |
No processing |
662 |
805 |
0,82 |
12,5 |
8,8 |
Ст3сп |
Heating 250ºС |
757 |
873 |
0,87 |
12,0 |
8,8 |
* With carbonitride hardening |
3. In the case of steel production, for example, in electric furnaces, the National Metallurgical Academy of Ukraine has developed and mastered the method of nitrogen introducing into steel using a nitrogen-containing compound with ferromanganese. Technology has been mastered in industry.
Proposal
1. To use in India nitriding of carbon and corrosion-resistant steels with gaseous nitrogen when flushing in a GOR unit.
2. Together to master the carbonitride hardening of steel by micro-alloying of Ti and Al for specific steel grades and specified mechanical properties.
3. To use nitrogen introducing with a nitrogen-containing compound together with ferromanganese in the case of steel production, for example, in electric furnaces.
Innovative Production Processes
- Production of functional and protective coatings.
- Manufacture of engineering products made of high-chromium iron-carbon alloys with nanostructured matrix.
- Ferrite (warm) rolling of extra-thin low-carbon and ultra-low-carbon steel for cold stamping or deep drawing.
- Modification of structural and piston alloys of the Al-Si system.
- Temporary anticorrosion protection of metal rolling.
- Processing of biomass and other organic wastes for obtaining charcoal, thermal and electric power.
Innovative Methods and Processes in Casting Industry
- Reduction of metal loss in supply riser.
- Inoculant for metallurgical equipment castings.
- Gas dynamic attack on metal in moulds.
- Production of high-quality castings made of remelted aluminium wrought alloy scrap.
- Production of rolling mills using complexly inoculated cast irons.
- Heat-resistance increase in castings made of complex alloyed and inoculated cast irons
- Gazars as a new type оf porous materials.
- Production of “solar” silicon with improved electro-physical properties.
- A composite material “cermet”.
- Alresist.
- Low-alloy vanadium-free steels with carbon nitride hardening.
Innovative Resource-Saving Technologies in Electrometallurgy of Steel and Ferroalloys
- Production of ferronickel and manganese ferroalloys.
- One-stage procedure of producing high-quality thermoanthracite in electric calcinator with high lining durability.
- Production of boron carbide.
- Production of graphite-like and wurtzite-like boron nitride.
- Automatic control system for the electric regimes of ferroalloy furnaces (ACSER).
- Production of low-carbon ferrosilicomanganese.
- Production of bearing steel with standardized ASTM E-45 amount of non-metallic inclusions due to specified chemical and mineral composition.
BLAST FURNACE OPERATOR`S PC: AN INTERACTIVE SYSTEM
IMPROVED TECHNOLOGY OF METAL DEGASSING BY GAS MIXTURES AT LADLE TREATMENT
THE RECEPTION TECHNOLOGY OF MECHANICAL ENGINEERING PRODUCTS FROM HIGH CHROMIUM IRON-CARBON ALLOYS WITH NANOSTRUCTURE MATRIX
PROCESSING OF BIOMASS AND OTHER ORGANIC WASTE TO PRODUCE WOODY COAL, HEAT AND ELECTRIC POWER
EFFECTIVE TECHNOLOGIES OF UTILIZATION OF METALLURGY AND MASHYNERY WASTES
NEW UNTOXIC PIGMENTS FOR ANTICORROSION PRIMERS
THE RADAR SYSTEM FOR MONITORING OF PROFILE CHARGE SURFACE IN BLAST FURNACE
DESIGNING AND MANUFACTURE OF NANOCOMPOSITE MATERIALS FROM CARBON NANOTUBES (CNT)
AUTOMATIC CONTROL SYSTEM FOR THE ELECTRIC REGIMES OF THREE-ELECTRODES (ACSEM-3) AND SIX-ELECTRODES (ACEMS-6) FERROALLOY FURNACES
TECHNOLOGY OF LOW - CARBON MANGANESE SILICON
TECHNOLOGY OF DEOXIDATION AND LADLE TREATMENT FOR HIGH STRENGH ROD WIRE MANUFACTURE
AUTOMATIC CONTROL SYSTEM FOR THE ELECTRIC REGIMES OF FERROALLOY FURNACES (ACSER)
INNOVATIVE TECHNOLOGY OF BORON CARBIDE PRODUCTION AND WURTZITELIKE AND GRAPHITELIKE BORON NITRIDE PRODUCTION
COLD CONTINUOUS DIE ROLLER ROLLING OF THE EXTRA-THINWALLED TUBES
PRECISION SEAMLESS TUBES TECHNOLOGY ELEMENTS OF PILGER ROLLING TECHNICAL AUDIT & INNOVATION
NEW TECHNOLOGY OF PRODUCTION "SOLAR" SILICON WITH INCREASED ELECTROPHYSICAL PROPERTIES
Innovation technology of functional and protective coatings manufacturing
HIGH EFFECTIVE COMPOSITE WELDING WIRE: TECHNOLOGY OF MANUFACTURE AND PROPERTIES
Alakh Singh - Assistant of the Rector of NMetAU (International Business)
alakh@metal.nmetau.edu.ua | +38(093)709-66-82 (Whatsapp)
Images
Applications
metal.mp4 (metal.mp4 49995 kb)